関西電力の挑戦。なぜ3Dプリンターで水車を?
四村川発電所の全景
水車発電機を収納しているハウジング(写真の中央)
和歌山県の紀南地方には、関西電力が維持・運用する水力発電所が計14箇所あります。そのうちのひとつが、2025年6月に運用開始から100周年を迎えた四村川発電所。関西電力は今、この四村川発電所を舞台に画期的な挑戦をしています。
それは金属3Dプリンターでつくった“水車ランナ”の運用です。
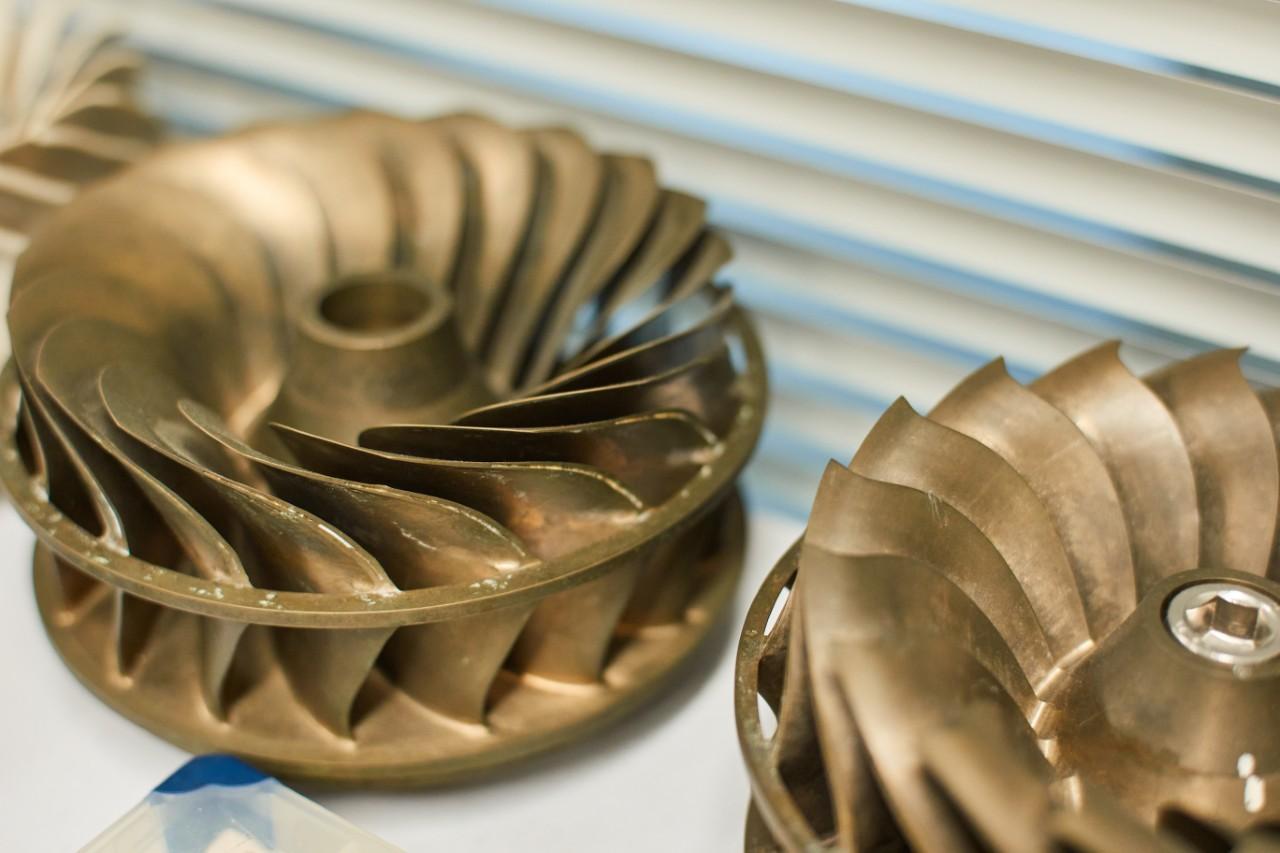
「水車ランナ」と呼ばれる羽根車
水力発電所では水が流れ落ちる落差を利用して発電をします。このとき水が流れ落ちるエネルギーを回転するエネルギーに変える流体機械を「水車」といい、水車内で水の力によって回転する羽根車を「ランナ」といいます。水が落ちる落差を使って発電機を回し、電気を生み出す仕組みですから、水力発電では水車ランナが一番大切な役割を担っているといえるかもしれません。
その水車ランナをいったいなぜ3Dプリンターでつくろうと考えたのでしょうか。さっそく関西電力のプロジェクト責任者と共同研究者である宮川教授に語っていただきましょう。
失敗を恐れず挑戦することで水力業界を進歩させたい
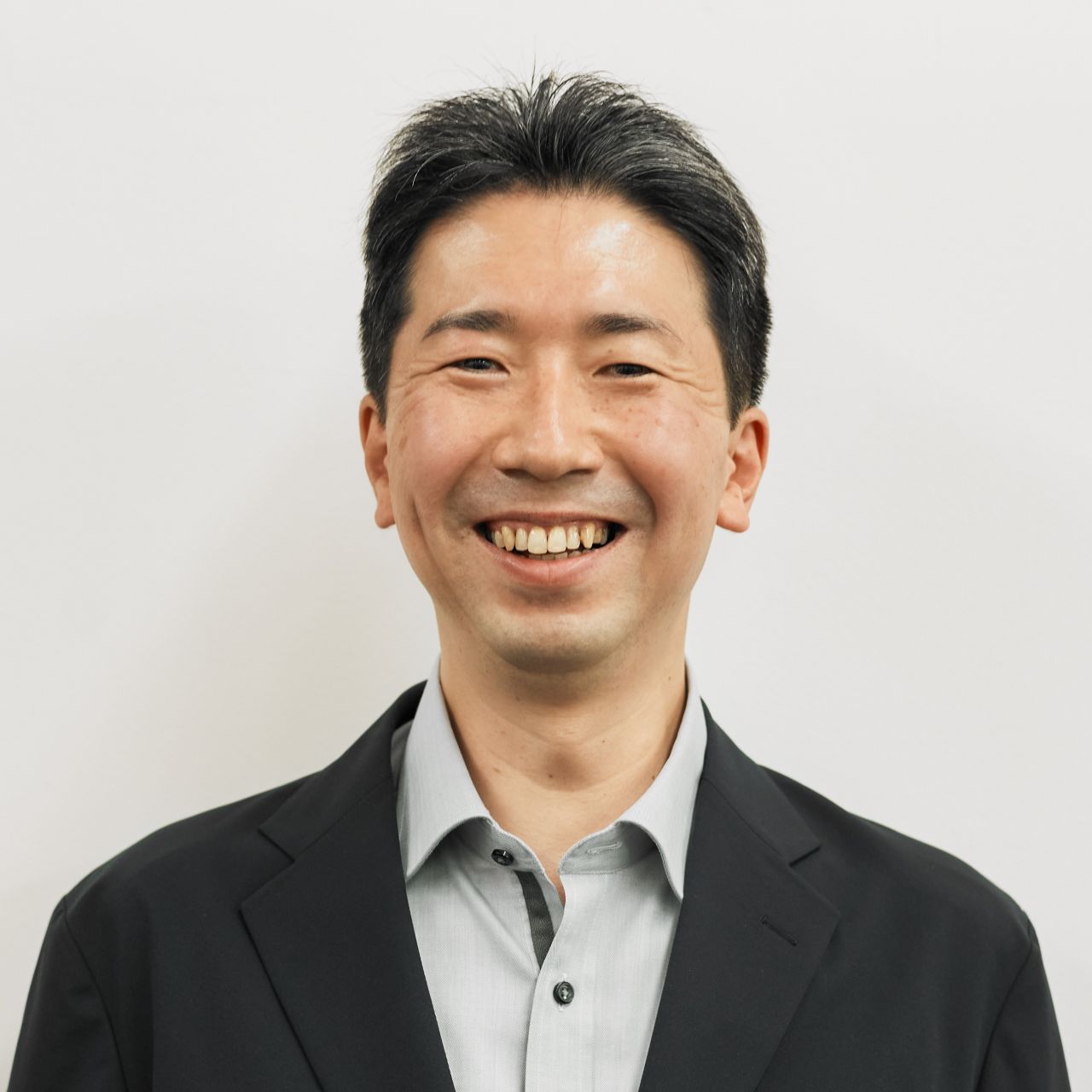
川田顕
関西電力 再生可能エネルギー事業本部 水力エンジニアリングセンター 国内水力グループ 総括課長
担当時代は、水力、変電設備保全運用、全社員対象研修の企画、東京支社などさまざまな業務を経験。役職以降は、水力事業の計画・運営、海外案件などに携わるなど水力事業中心のキャリアを歩み、黒部の事業所での勤務経験も。気象予報士の資格保有者といった一面も。
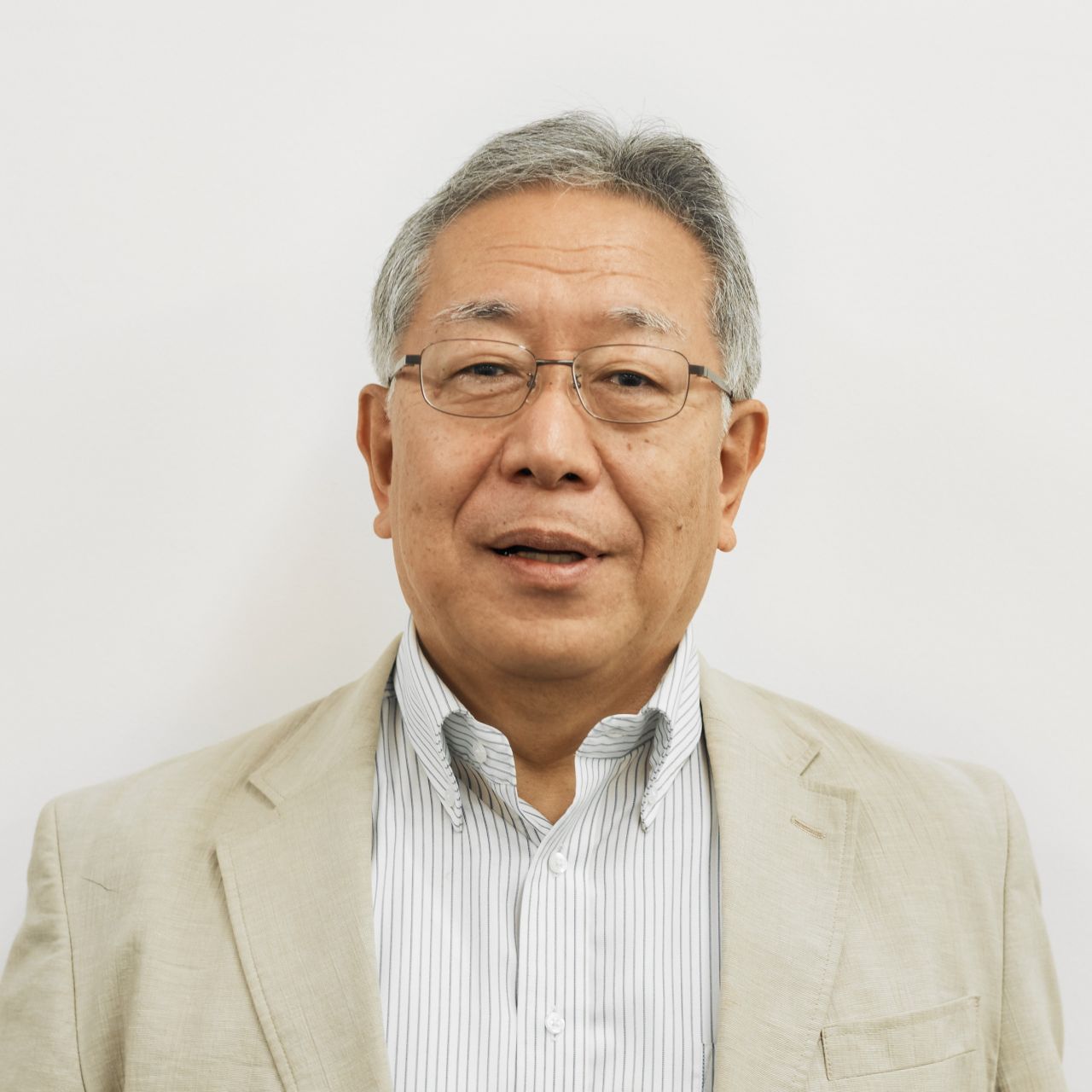
宮川和芳教授
早稲田大学 理工学術院 基幹理工学部 教授
三菱重工業で26年間にわたり、技術本部の高砂研究所で流体機械などの開発に従事。その後、早稲田大学に移り、現在は基幹理工学部で教授を務める。産業界での豊富な経験を活かし、水車、ポンプ水車やポンプの研究に取り組む。日本機械学会、ターボ機械協会などでも要職を歴任し、産学連携にも注力。

水車ランナ設計への想いを語る
宮川教授「私は流体機械が研究テーマで、水車やターボポンプなどの研究や開発に長年従事してきました。そうしたキャリアを耳にした川田さんが、2023年7月に早稲田大学の私の研究室を訪ねてきたのがプロジェクトの始まりでしたね」
川田「はい。この挑戦を成功させるには宮川教授のご協力が不可欠だと考えてお会いしに行きました。そもそも、従来の水車ランナは電力会社がメーカに設計段階から開発を依頼し、一つひとつの水車ランナを鍛造や鋳造といった方法で製作してきました。つまり、水車ランナというのはその多くが一品一様で、特注品なのですよね」
宮川教授「発電所ごとに水が流れ落ちる落差、水の流量などが異なりますから、水車は地点や要望に合わせて個別かつ高品質に製作する一品一様のケースがほとんどです」
川田「その点、3Dプリンターは一品一様の形状をスピーディに製造するのにとても有効で、一度試してみたいと思っていました。また、3Dプリンターを使えば設計の自由度が高まり、これからの水車ランナの設計を大きく変えることができるのではないかと期待も持っていました」
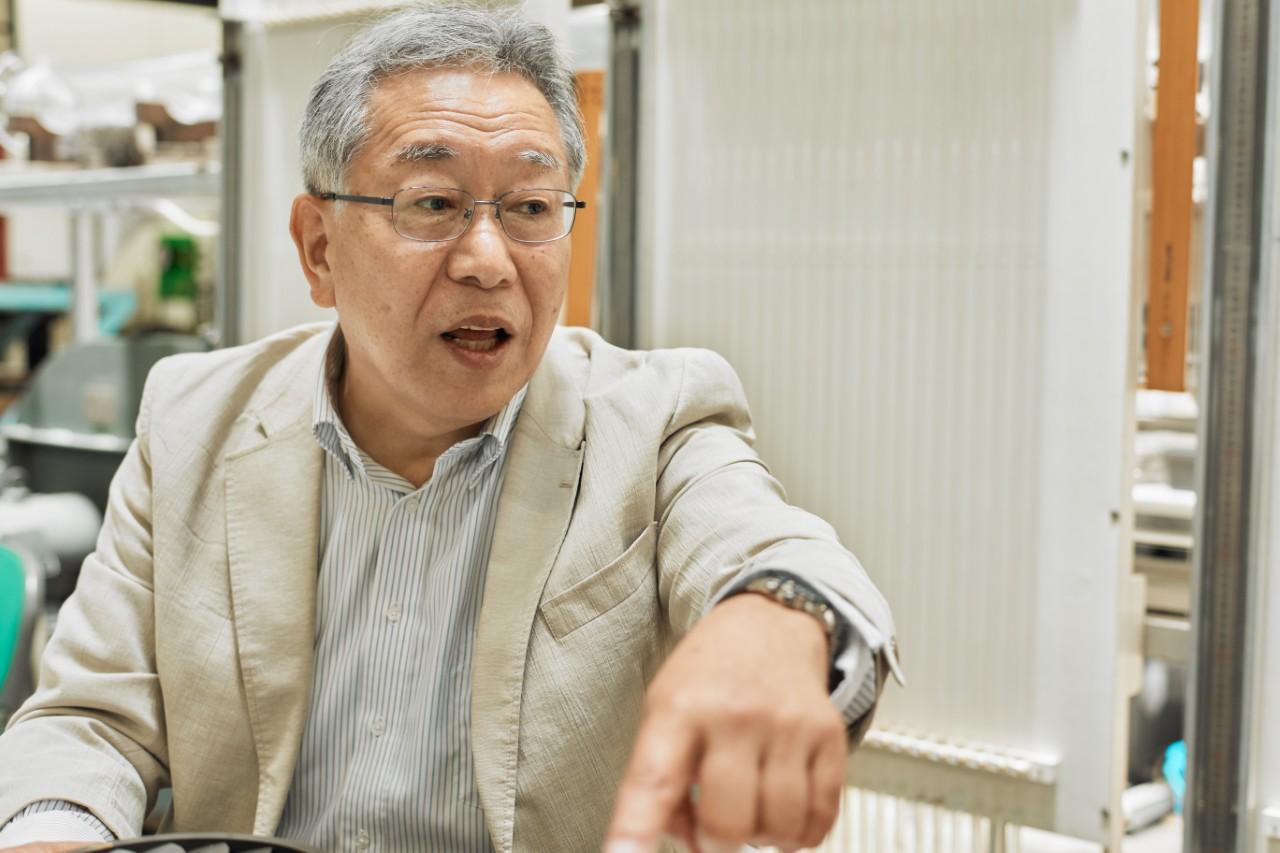
宮川教授「ただし、通常の樹脂製3Dプリンターでは事業用に足る水車ランナをつくるのは難しい。一般的な3Dプリンターは、細長い紐状の樹脂を熱で溶かして一層ずつ積み上げて造形する場合が多いですが、樹脂製ではそもそも水の力に耐えられず変形や破損が生じてしまったり、土砂摩耗などの要因で水車ランナがすぐに傷ついたりして使い物になりません」
川田「例えば、関西電力は水の宝庫である黒部川水系や木曽川水系などに多くの水力発電所を所有していますが、そういった激しい流れの河川では、岩が削られて砂粒になり、その粒が水車に入り込みます。そういった土砂による摩耗により樹脂製でなくステンレス製の水車ランナであっても傷だらけになり、5年程度で交換が必要になってしまう場合もあるのです」
宮川教授「今回の水車ランナ取替前の四村川発電所は、川から流れてくるどんぐりや木片などが水車ランナによく詰まっていたようですね」
川田「四村川発電所は当社の水力発電所の中では小さいサイズであることもあり、川から流れてくるどんぐりや木片などが水車ランナに詰まりやすいため、年間10回程度は運転を2〜3日停止して清掃を行っていました。これでは現場の負担が大きくなるだけでなく、発電電力量も減少してしまうということがここの現場の課題としてあったため、せっかく製作するのであればそれも解決したいと考えました」
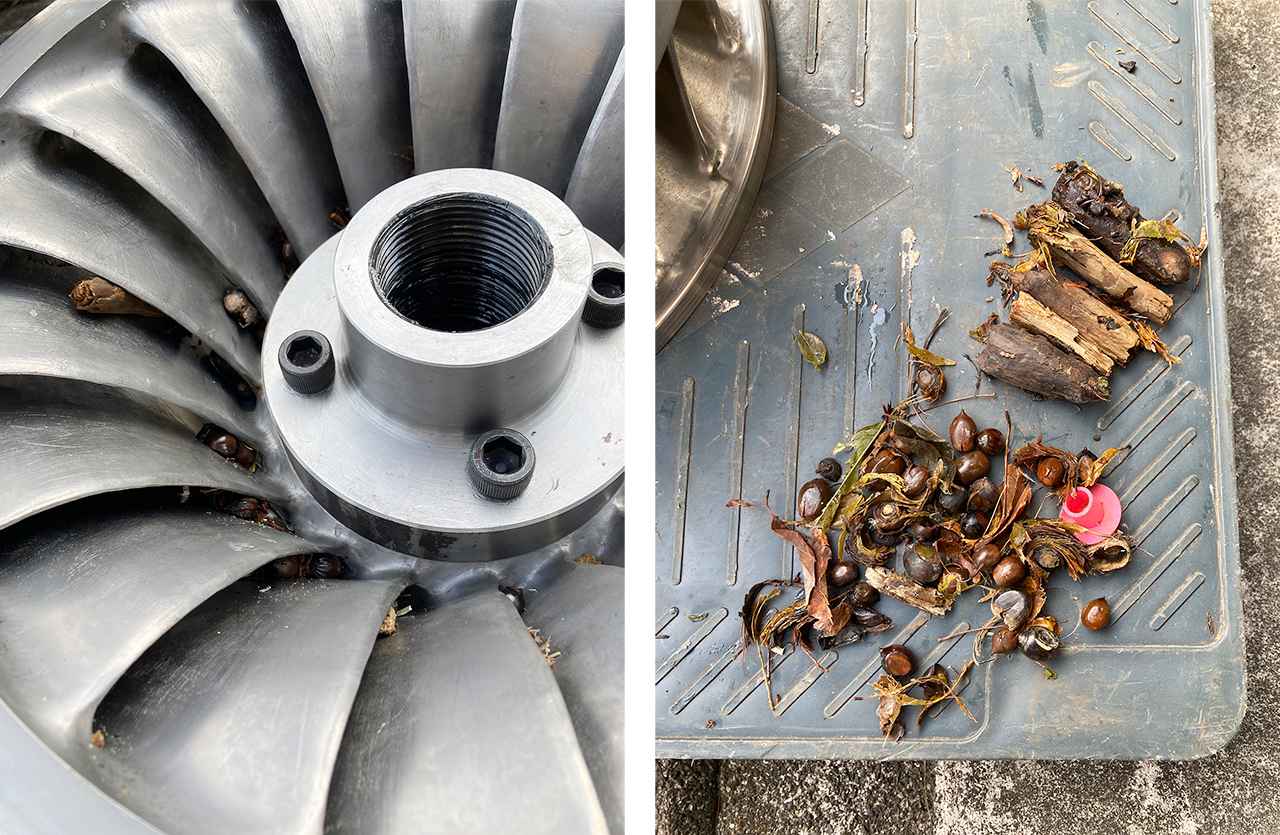
従前の水車ランナ(写真左)と実際に詰まっていたどんぐりや木片など(写真右)
宮川教授「そこで川田さんが考えたのが、樹脂の代わりに金属を素材に使う方法でした。つまり、“金属3Dプリンター”で水車ランナをつくるというアイデアです。この方法であれば、素材によっては耐久性が高く、土砂摩耗に強いものを作れるというだけでなく、金属3Dプリンターならではの設計の自由度を活かしてどんぐりや木片が詰まりにくい設計の水車ランナをつくることできるかもしれないと考えたのですね」
川田「はい。ただ、金属3Dプリンターで作った水車ランナを事業用の水力発電所に導入したという話はこれまで聞いたことがありませんでした。そういう意味では前例のない話だったので手探りで進めるしかなく、失敗する可能性もありました。しかし、リスクがあったとしても、せっかくこんな製造技術のゲームチェンジャーになる可能性のあるものがあるのに、誰かが挑戦しなければ水力業界が進歩しない。だったら、それをするのは関西電力でありたいと考えました。その点を快くご理解いただいた宮川教授には本当に感謝しかありません」
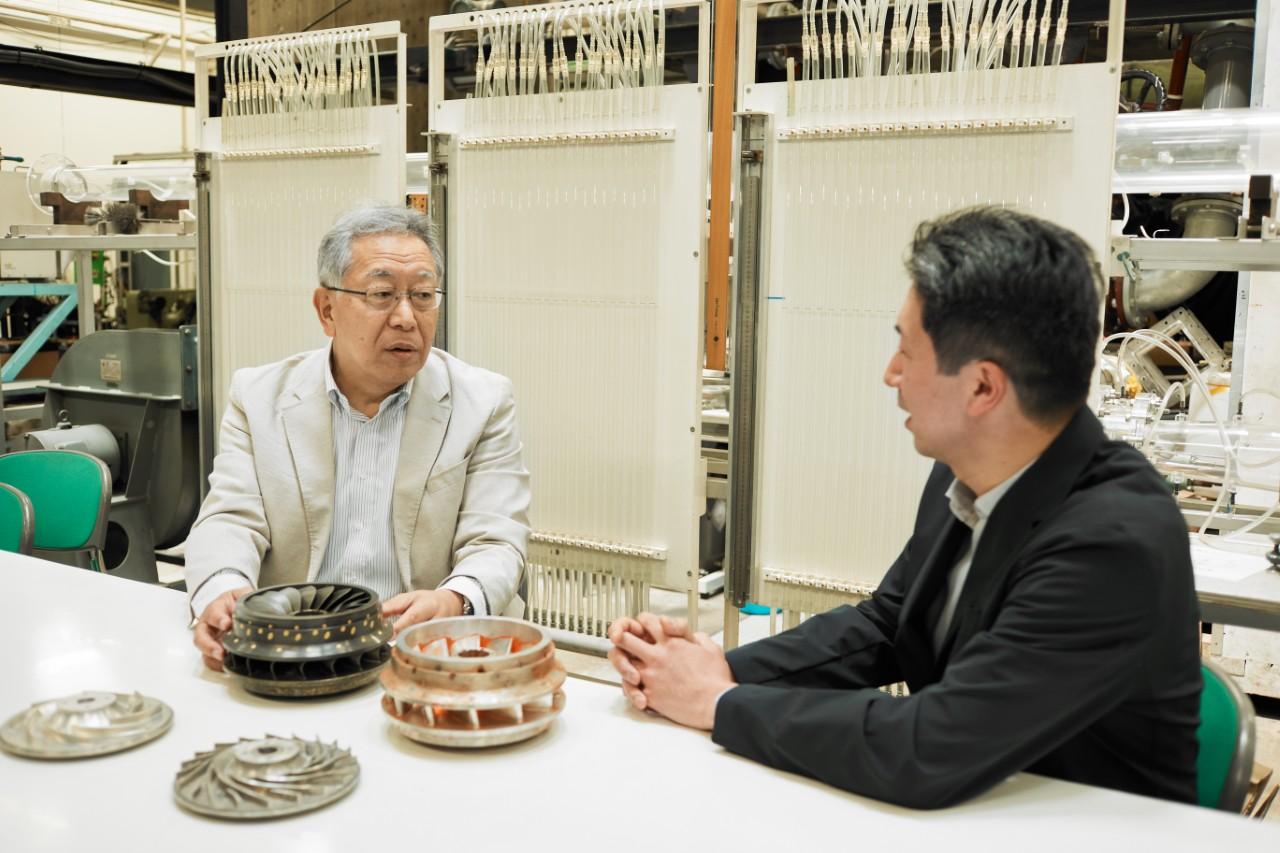
宮川教授がこれまでに設計した水車ランナの模型などを前に
宮川教授「失敗のリスクがあると、新たな挑戦に躊躇してしまうものですが、川田さんはやるんだったら世界初であろうものを目指してみましょうと水力の将来への想いを熱く語って、失敗するかもしれないのに思い切って崖から飛び降りてくれた(笑)。リスクを恐れず最初に行動を起こす人を“ファーストペンギン”といいますが、まさに最初に海に飛び込んだ勇気あるペンギンです。今まで数多くの電力会社の方とお会いしてきましたが、正直なところ川田さんみたいな方とお会いしたことはありませんでした」
素材もすごい!ロケットにも使われる超合金とは?
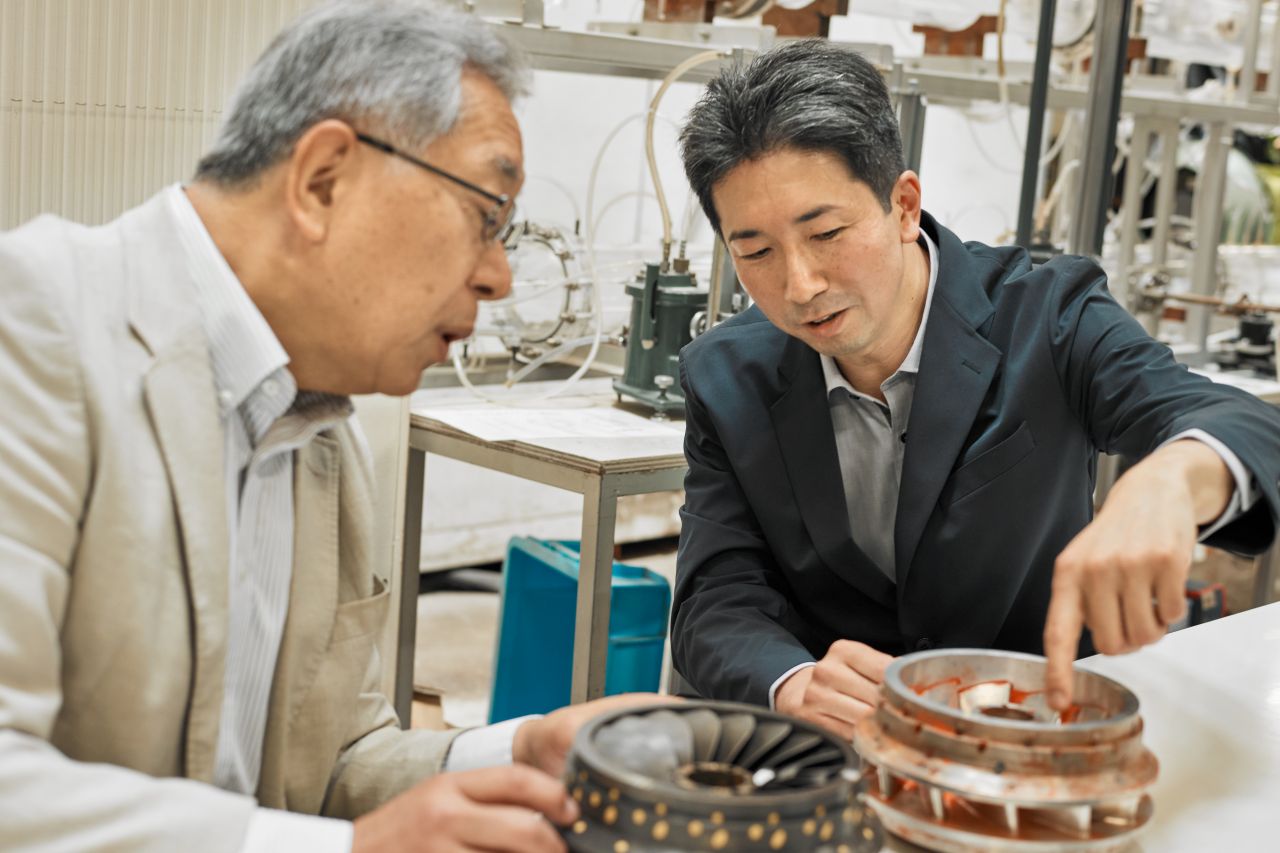
水車ランナの設計や材質についての想いを語る
今回のプロジェクトには、金属3Dプリンターで水車ランナをつくること以外にもうひとつ、おそらく世界初の大きな挑戦がありました。それは、水車ランナの素材に「インコネル」と呼ばれるニッケルを基盤とする超合金を使ったことです。
川田「多くの水車ランナは素材にステンレスを使っています。ステンレスは材料費が比較的安く、加工がしやすいというメリットがあるからです。水車ランナの複雑な構造をこれまでの削り出し加工などで造形するためには、素材にある程度の加工のしやすさが必要になるためです」
宮川教授「一方で、ステンレスは素材の強度や土砂摩耗などに対する耐久性において問題が発生する場合もありました。先ほどのお話のように、河川によっては、ステンレス製では使用していると土砂摩耗で羽根が傷つき、発電効率が落ちてしまい、取り替えなければならなくなる場合もあります。そこで我々が金属3Dプリンターでつくる水車ランナの素材に選んだのがインコネルでした」
川田「素材をインコネルにしてみようということは即断しました。ちなみにインコネルはロケットにも使用されているそうですね」
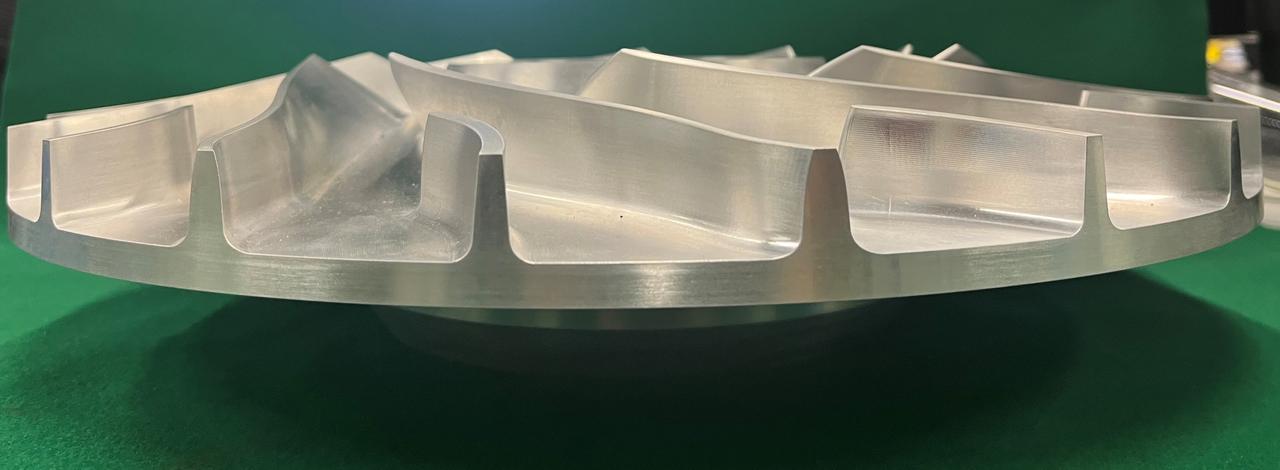
宮川教授が研究されているロケット用ターボポンプの羽根車
宮川教授「ロケットエンジンや航空機エンジン、原子力発電所、化学プラントなど、高温高圧の過酷極まりない環境で信頼性が問われる部分に使用される超合金です。ちなみにロケットエンジンのターボポンプに送り込まれる燃料はなんとマイナス253℃なのですよ。高温だけじゃなく、低温にも強い高強度の素材です。これほど強度の高い材料が事業用水力発電所の水車ランナに使用されたことは世界で初めてのことだと思います」
川田「素材をインコネルにすることにより土砂摩耗等の要因で水車ランナが傷ついたりする心配がなくなるのではないかなと考えましたが、本当にその通りになりそうです」
宮川教授「水車ランナが傷つく大きな原因がもう一つあります。水車内部では“キャビテーション”といって、圧力の急激な低下によって液体内に気泡が発生し、また急激に崩壊する衝撃圧力により水車ランナの表面が損傷する現象が起こる場合があります。本研究で、強制的にキャビテーションを発生させ金属表面の損傷状況を観察する実験をしてみた結果、インコネルだとキャビテーションによる損傷がほとんど現れませんでした。本当に驚くほど強い」
川田「そんなに強い素材なら、ほかの水車ランナにもインコネルを使用しておけばいいじゃないかと思うかもしれせんが、インコネルはものすごく硬いので、従前の鍛造といった削り出しの製造方法などでは、コストが高くなりすぎたりしてとてもじゃないけど導入できなかったですね」
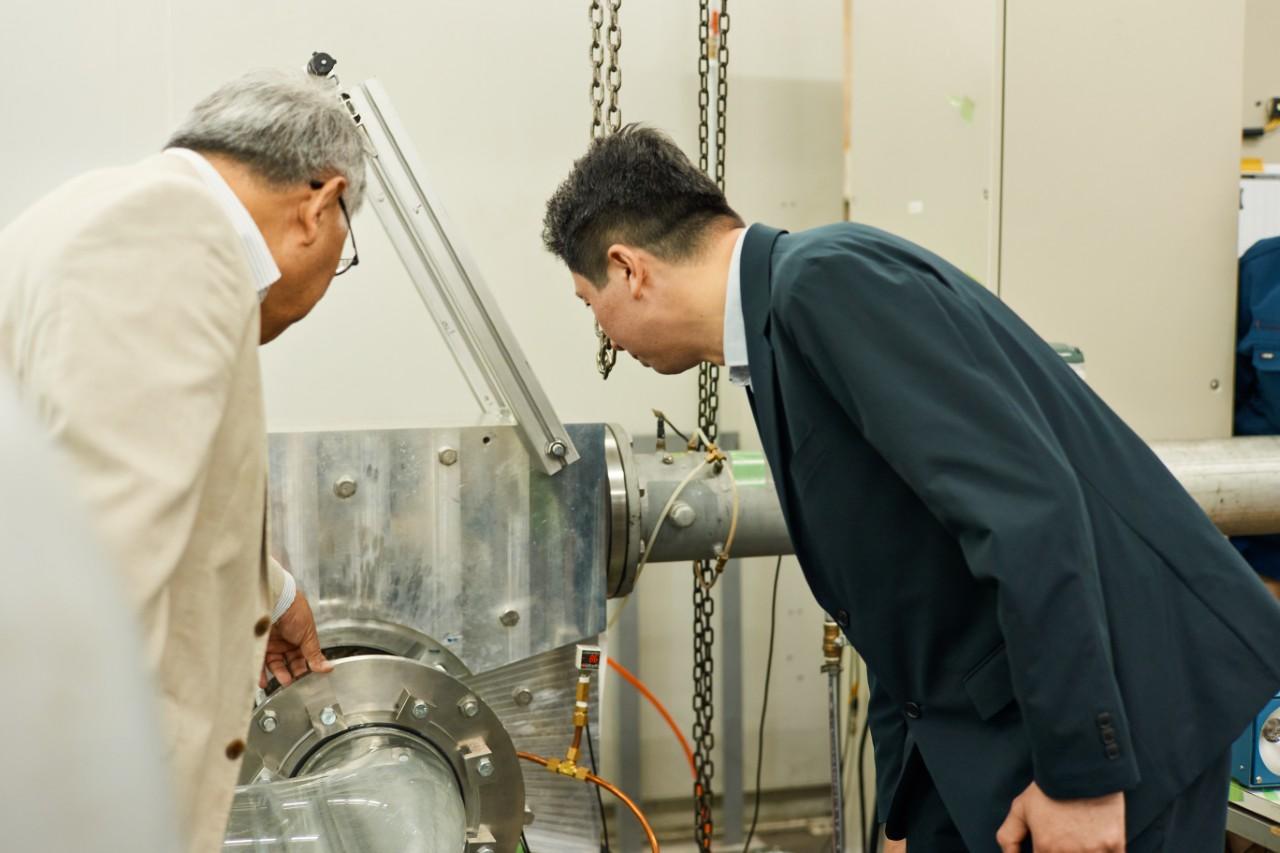
金属3Dプリンターで製作した模型水車ランナの試験を行った装置を確認しているところ
宮川教授「今回、金属3Dプリンターで挑戦したからこそインコネルを材料に使うことが可能になった。普通の樹脂製の3Dプリンターと違い、金属3Dプリンターは金属粉末を層状に敷き詰め、一層、一層焼きながら積み重ねていきます。その製造過程での管理、後処理等含めて試行錯誤をしながら製作したこともあり、今回は3カ月弱かかりました」
川田「とはいえ、サイズにも寄りますが従来の方法による水車ランナの製作は1年程度かかりますから、金属3Dプリンターでの製作により製作期間もかなり短縮できた形です。今後、技術が進歩すれば、1カ月かからずに製作できるようになるかもしれません」
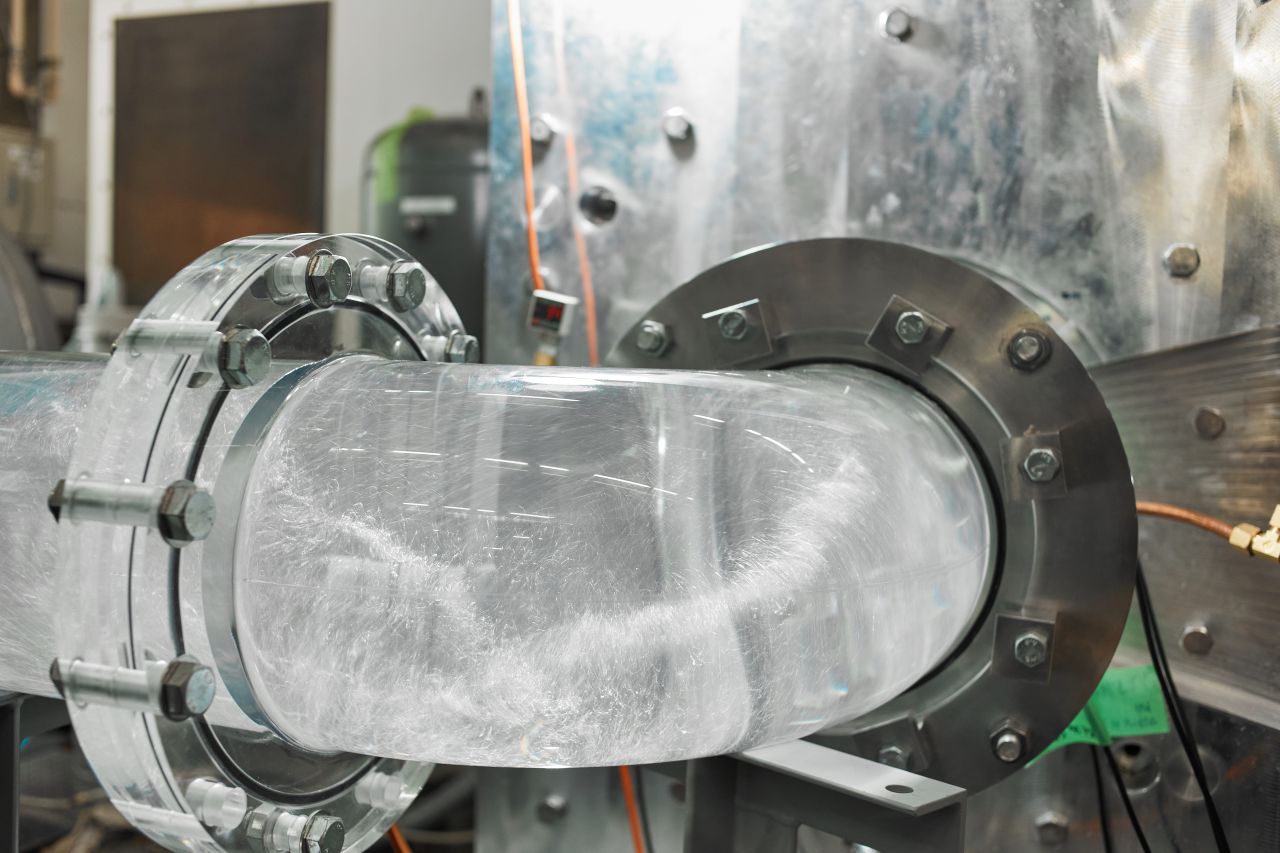
宮川研究室では様々な水車に関する研究が日々行われている。写真はホワールと呼ばれる水車ランナ出口に発生する渦
宮川教授と川田家二代のコラボレーションによって欲張り水車ランナが完成!
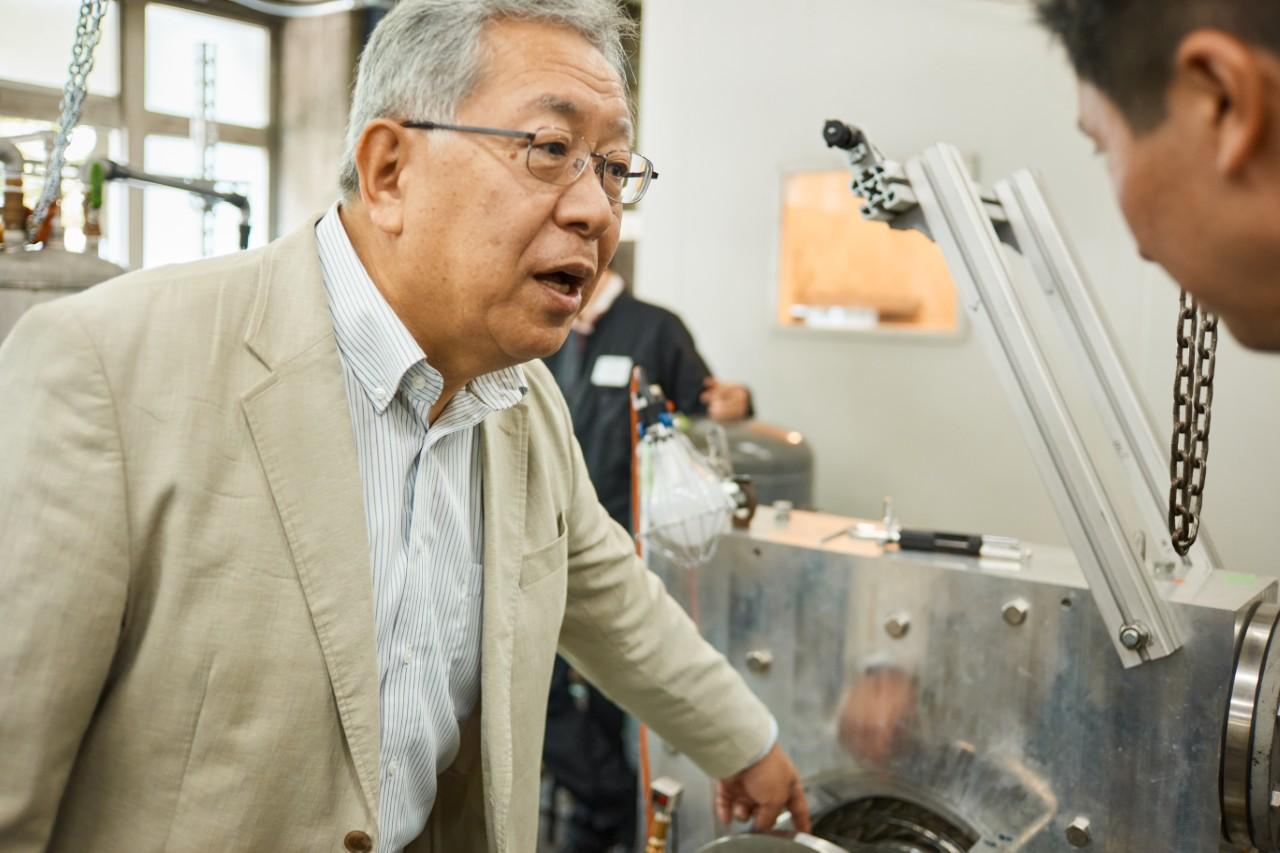
川田と宮川教授は2023年7月に行われた最初のミーティングが初対面でした。ところが、この挑戦を成功させるために議論を重ねるなかで、2人の思わぬ接点が明らかになります。それは運命とも必然ともいえるドラマティックな接点でした。
川田「宮川教授にお会いをし、いろいろお話をさせていただくなかで本当に驚いたのは、私の父親との関係でした。宮川教授は、三菱重工の発電用ガスタービンやポンプなど大型回転機械の研究開発拠点である高砂研究所のご出身ですが、実は私の父親も三菱重工出身で、まさに高砂研究所にいたのです」
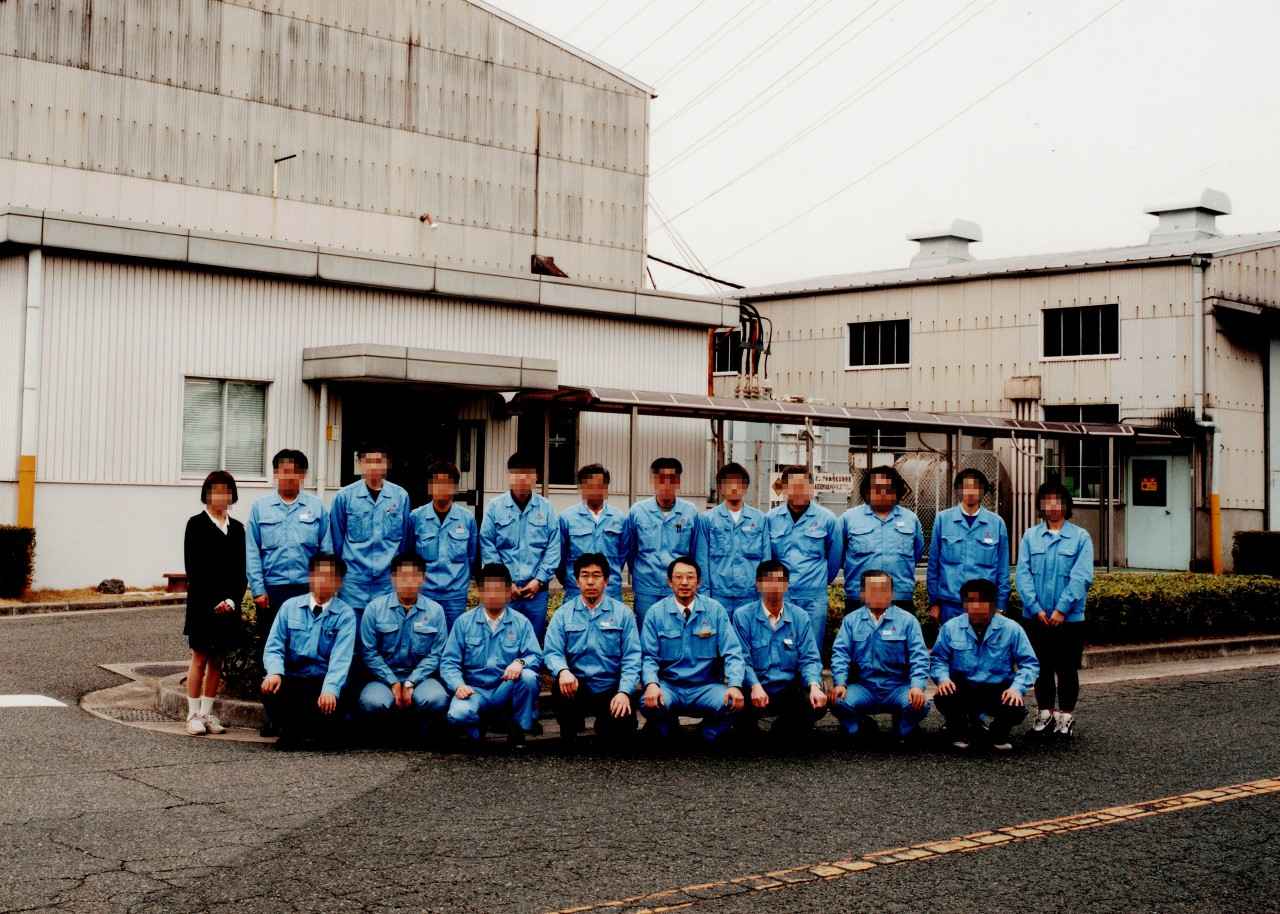
三菱重工 高砂研究所時代の宮川教授(前列中央左)と川田の父(前列中央右)
宮川教授「そうお聞きして『お父さんは高砂研究所で何をされていたのですか?』と私が質問したのですよね。高砂研究所には川田姓の方が何人かいましたから。そうしたら『ガスタービンのブレードの研究をしていたと記憶しています』と…。その当時、私も水車やポンプの研究開発をする研究室で働いていて、川田さんのお父さんはその研究室の室長でした。つまり、お父さんを知っているとかのレベルではなく、川田さんのお父さんは当時の私の直属の上司だったのですよ! しかも20年間くらい一緒に仕事をさせていただきました。さらに、川田さんのお父さんのデスクは私の隣だったこともあるのです」
川田「信じられないめぐり合わせですよね」
宮川教授「関西電力の原子力発電所のポンプシステムは三菱重工の製品が多いと思うのですが、そのほとんどに川田さんのお父さんの研究・開発が適用されているといっても過言ではありません。また、イギリスの機械学会でも栄誉ある賞を受賞するなど、三菱重工の川田さんといえば、今もウィキペディアがあるくらいで流体機械の分野では知らない人がいないくらいです。それほどすごい人だったのです」
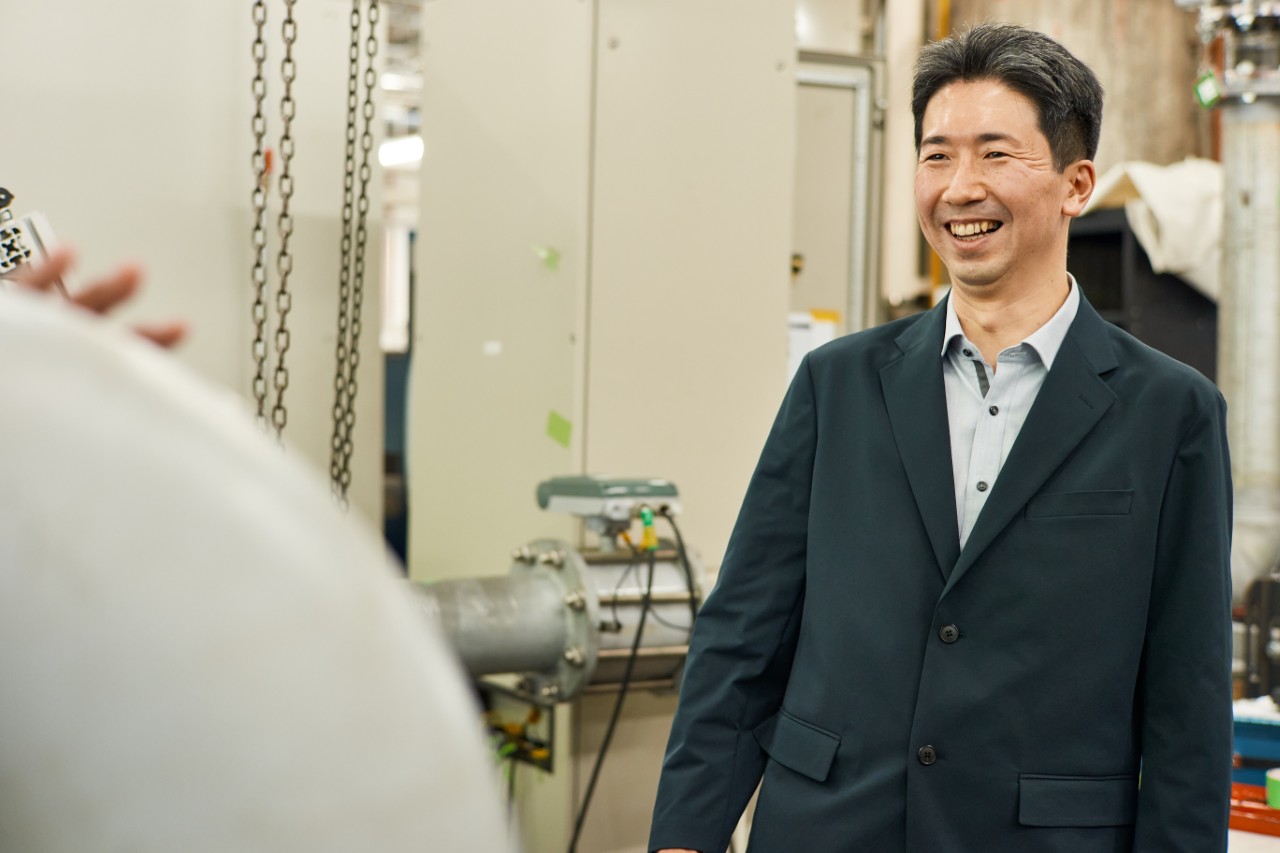
川田「それを息子は何も知らなかった(笑)。いえ、親子仲が悪いわけでは決してないです(笑)。仕事の話はお互いしないというか…」
宮川教授「実は、川田さんのお父さんとの関わりは今回のプロジェクトにも活かされています。例えば、今回の水車ランナには、四村川発電所クラスのサイズの水車ランナではほとんど前例のない“スプリッタランナ”を採用しました。主羽根と主羽根の間に小さな中間羽根を設けるタイプの水車ランナです。水車ランナにゴミなどが詰まらないようにするための一番簡単な方法は、主羽根の枚数を減らして主羽根と主羽根の間隔を広くすることですが、それでは効率が落ちてしまいます。ゴミが詰まらず、性能も低下しないようにしなければいけない」
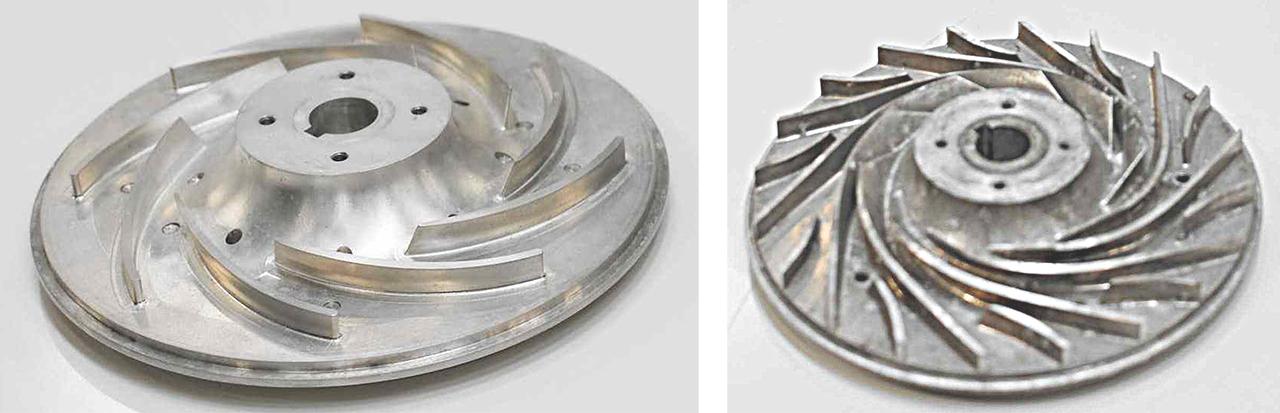
主羽根のみ(左)と主羽根と中間羽根(右)のイメージ
川田「私が欲張りだからそういうムチャなお願いをしたのですよね。3Dプリンターでの製作だからこそできる設計自由度を活かした、ゴミは詰まりにくいが、効率は落ちない水車ランナを目指したいと」
宮川教授「この難題を解決するための方法として採用したのがスプリッタランナです。スプリッタランナというのは、川田さんのお父さんが率いていた当時の研究室が研究していたもので、1990年代にはスプリッタに関する論文も発表しました。当時の研究結果が今回の水車ランナのベースになっているのですよ」
川田「しかし、単に中間羽根を設けるだけじゃなく、ゴミが詰まらず効率も低下しないように中間羽根の形状を最適化してくださったのは宮川教授です。宮川研究室の学生さんたちが高性能のコンピューターを使い、どういった形状にすれば効率が上がるか、半年間くらい取り組んでいただいたと聞いています」
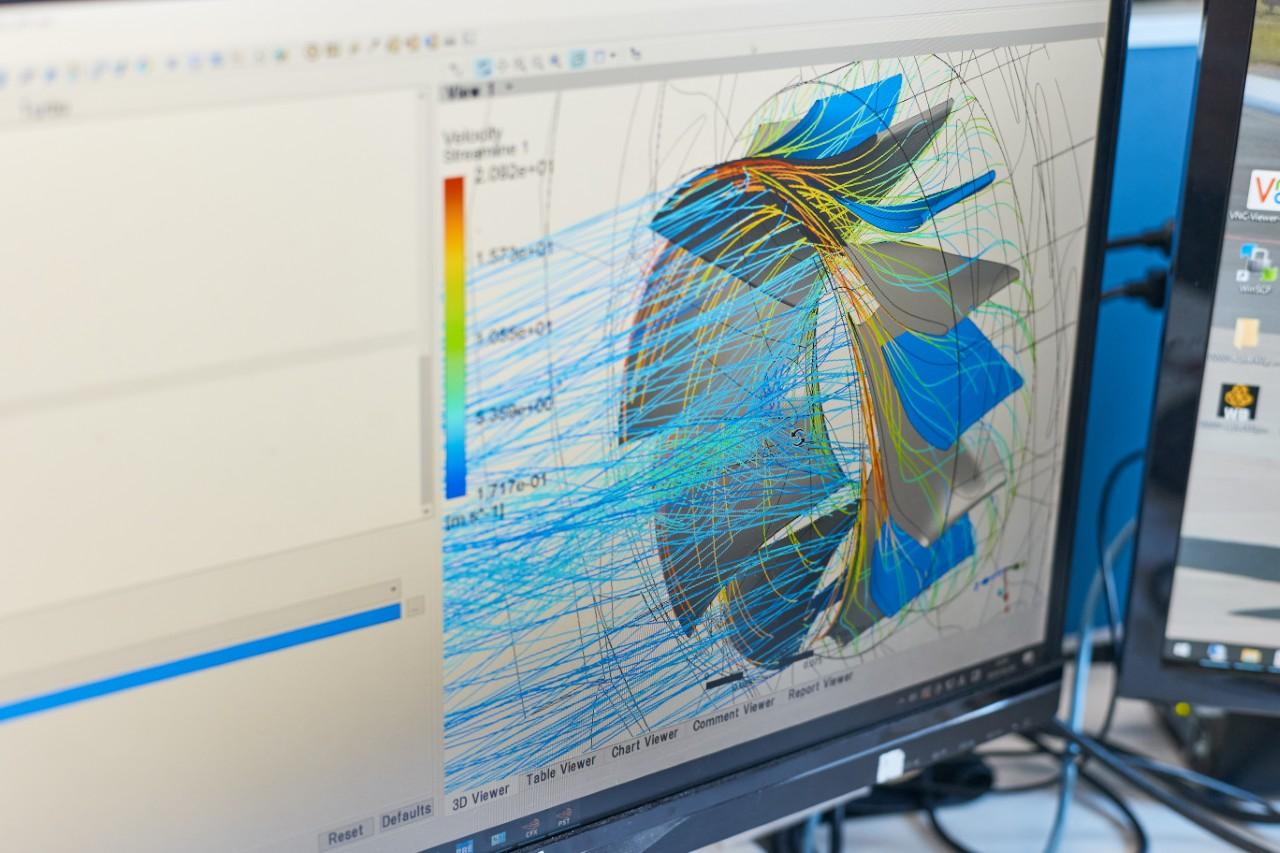
宮川研究室の学生さんたちがコンピューターでシミュレーションし最適な羽根を設計したといいます
宮川教授「たしかに大変な作業でした。スプリッタランナを最適化するために、設計した羽根によるシミュレーションを100回近くやったと思います。小さな失敗やトラブルもたくさんありました。しかし、私は三菱重工時代に川田さんのお父さんに流体機械についてはみっちり仕込まれていますので、どんなトラブルが起こりうるかある程度予見できますし、対処方法もわかっています。そういう意味では、今日は川田さんのお父さんにもお越しいただいて三者対談でも良かったかもしれません(笑)」
川田「三者対談はまたぜひ! 父はともかく、宮川教授の何十年にもわたる研究開発の蓄積があったからこそ今回の挑戦が成功したのだと思います」
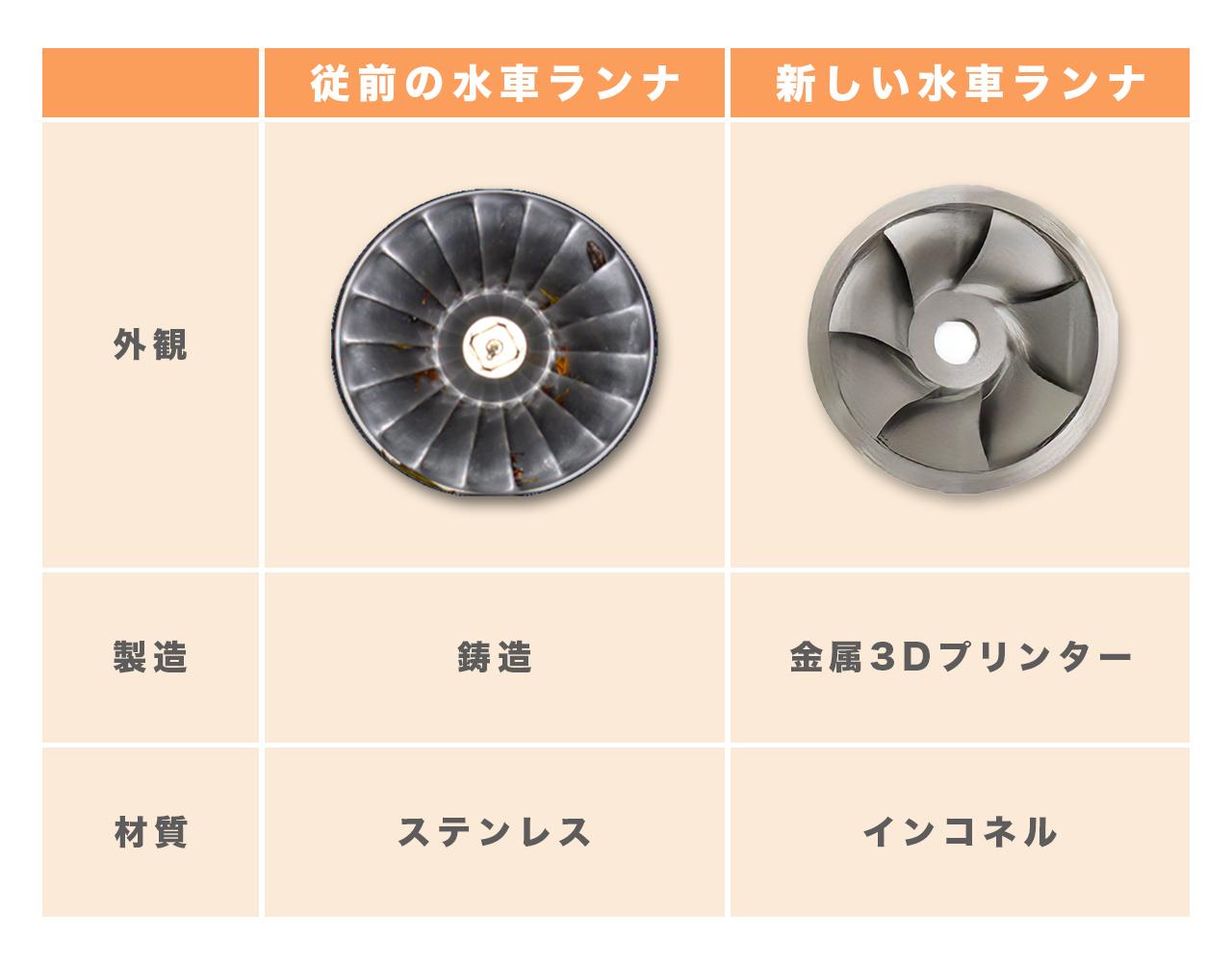
水力業界全体が注目!関西電力の挑戦は続いていく
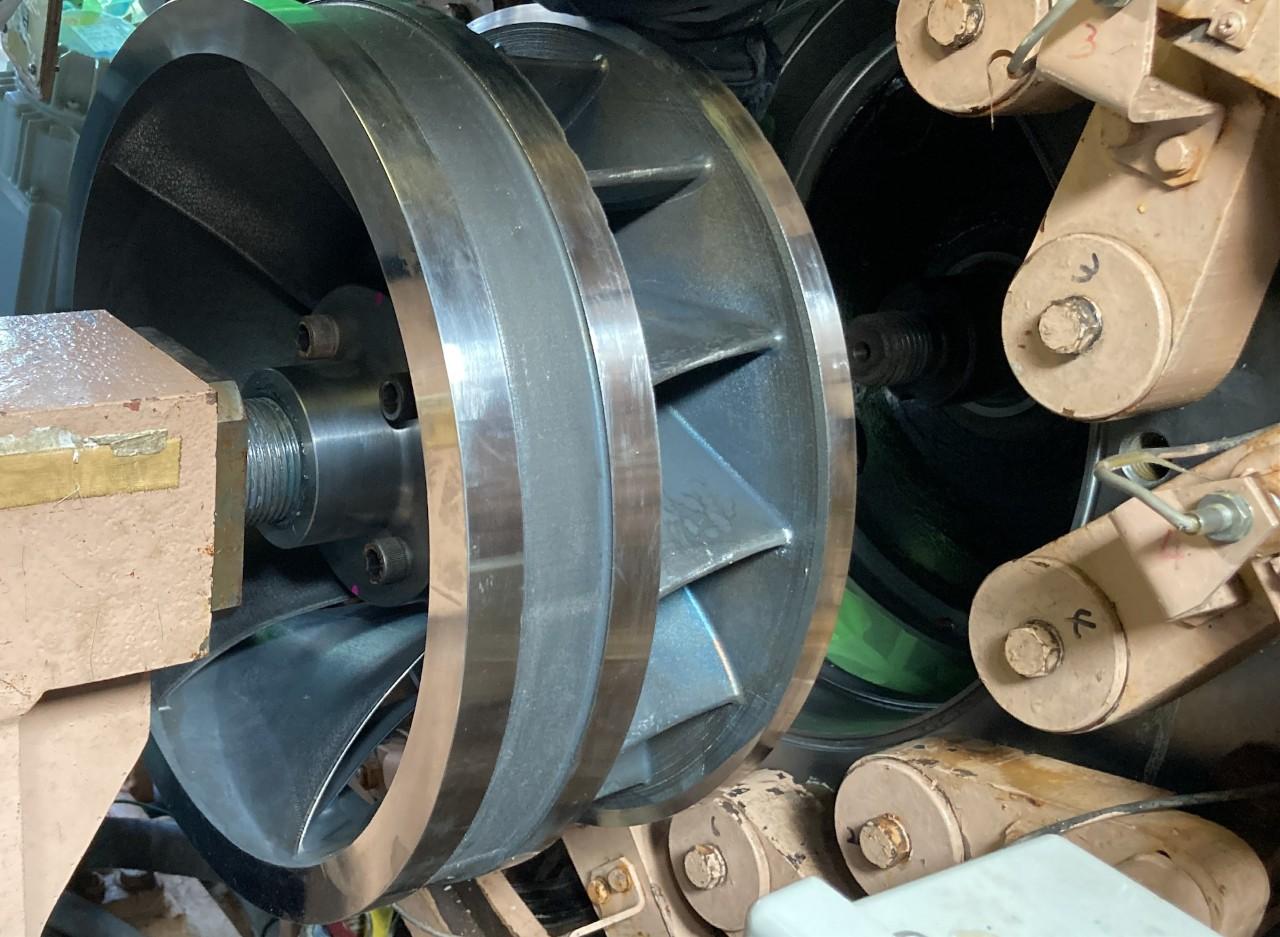
四村川発電所に据え付けられる金属3Dプリンターで製作したインコネル製水車ランナ
金属3Dプリンターでつくった水車ランナの実運用が四村川発電所でスタートしたのは2025年2月でした。プロジェクト責任者の川田によると、製作にかかった費用は従前の鋳造で製作したステンレス製水車ランナと大差なく、更に従前はゴミ詰まりがひどかったのが新しい水車ランナには何も詰まっておらず、現場からは喜ばれているといいます。
リスクを恐れず取り組んだ史上初の挑戦は見事成功したといっていいでしょう。そうなると、気になるのは今後の展開です。
川田「今回の挑戦のポイントは、金属3Dプリンターを使って水車ランナという水力発電所中で一番形状が難しいものの製造に取り組んだことでした。水車ランナをつくることができるなら、水力発電所のほかの部品はもっと簡単につくることができるはずです」
宮川教授「川から流れてくるゴミが詰まるのは水車ランナだけではありません。たとえば、水の流れを調整して出力や効率を調節する“ガイドベーン”という羽根なども、土砂が混入すると損傷してしまう場合などもあるなど、耐久性が非常に重要になる部品もいろいろあります」
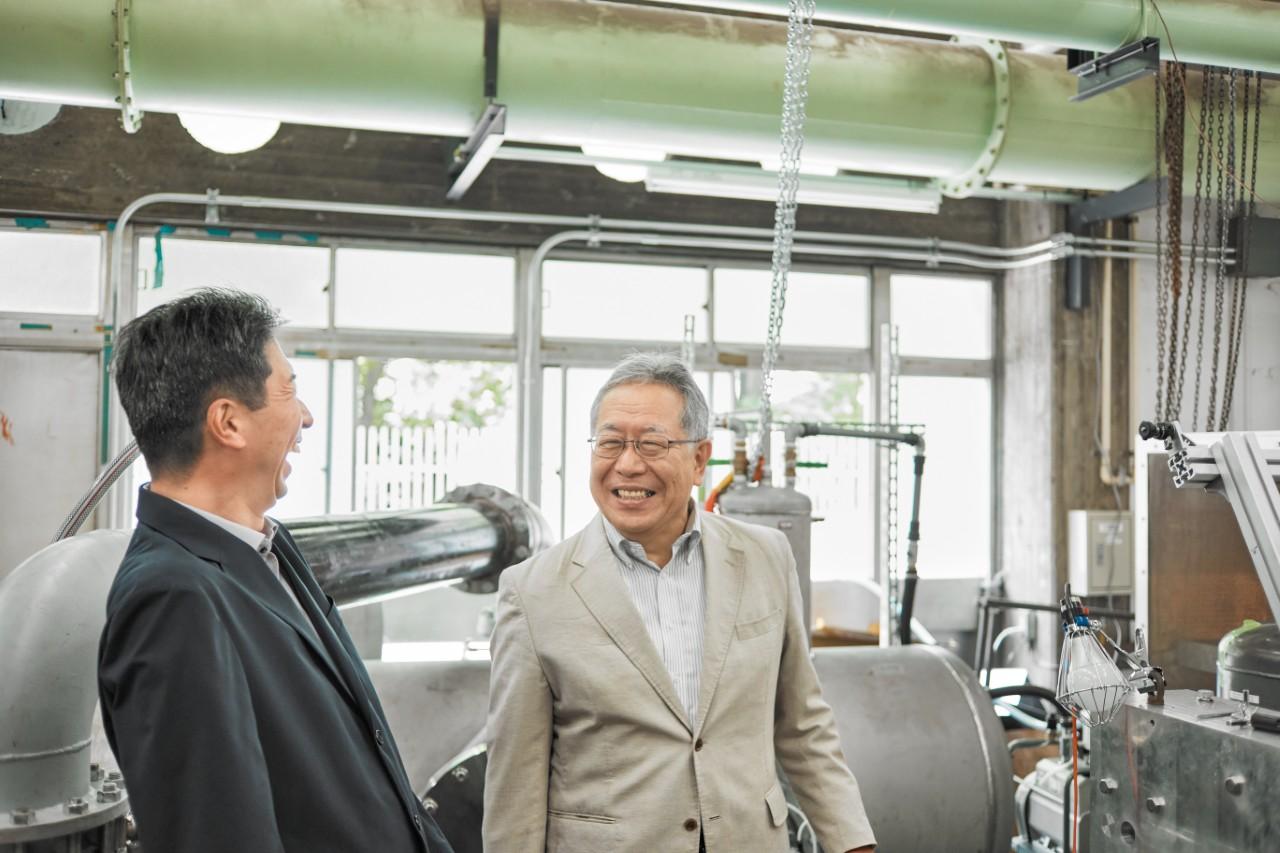
川田「これまでは、そういった部品が損傷するとメーカの工場に運んで修理していました。修理するために海外の工場まで運んだようなケースもあります。当然、その間、発電できなくなるのですが、そうした部品を金属3Dプリンターでつくることが一般化すれば復旧のための期間は格段と短くなります。将来的に技術が進歩して現場に金属3Dプリンターをもっていけるようになれば、破損した部品をその場で金属3Dプリンターを使って新しく製作してすぐ修理ができる、そんな世界になれば設備保全の現場では今とは異なる景色が広がるだろうと思います。まだまだ挑戦してみたいことはいっぱいありますので、宮川教授、これからも一緒に水力業界を『あっ!』と驚かせていきましょう!」
宮川教授「もちろん! ご一緒に! 現状では金属3Dプリンターでつくれる水車ランナのサイズに制約がありますが、金属3Dプリンターの世界は日進月歩ですから、さまざまな産業分野でどんどん進化していっています。今後は金属3Dプリンターの進化にともなって、もっと大きなサイズの水車ランナもつくれるようになるでしょう。それ以上にこれまでの鋳造、鍛造といった製造方法に合わせた水車設計から、3Dプリンターでの製造の自由度に合わせた水車設計へと水車設計の考え方自体が大きく変わっていく可能性も秘めていると思います」
川田「今回の挑戦で水力業界での金属3Dプリンターに対する注目度も高まるでしょう。関西電力にできたのなら、うちにもできるはずだって。そうやって水力業界全体が活性化して、進歩していくことはとても素晴らしいことだと思います。今度は関西電力が遅れをとったということにならないよう、これからもいろいろな新しい挑戦を続けていきたいと思います」
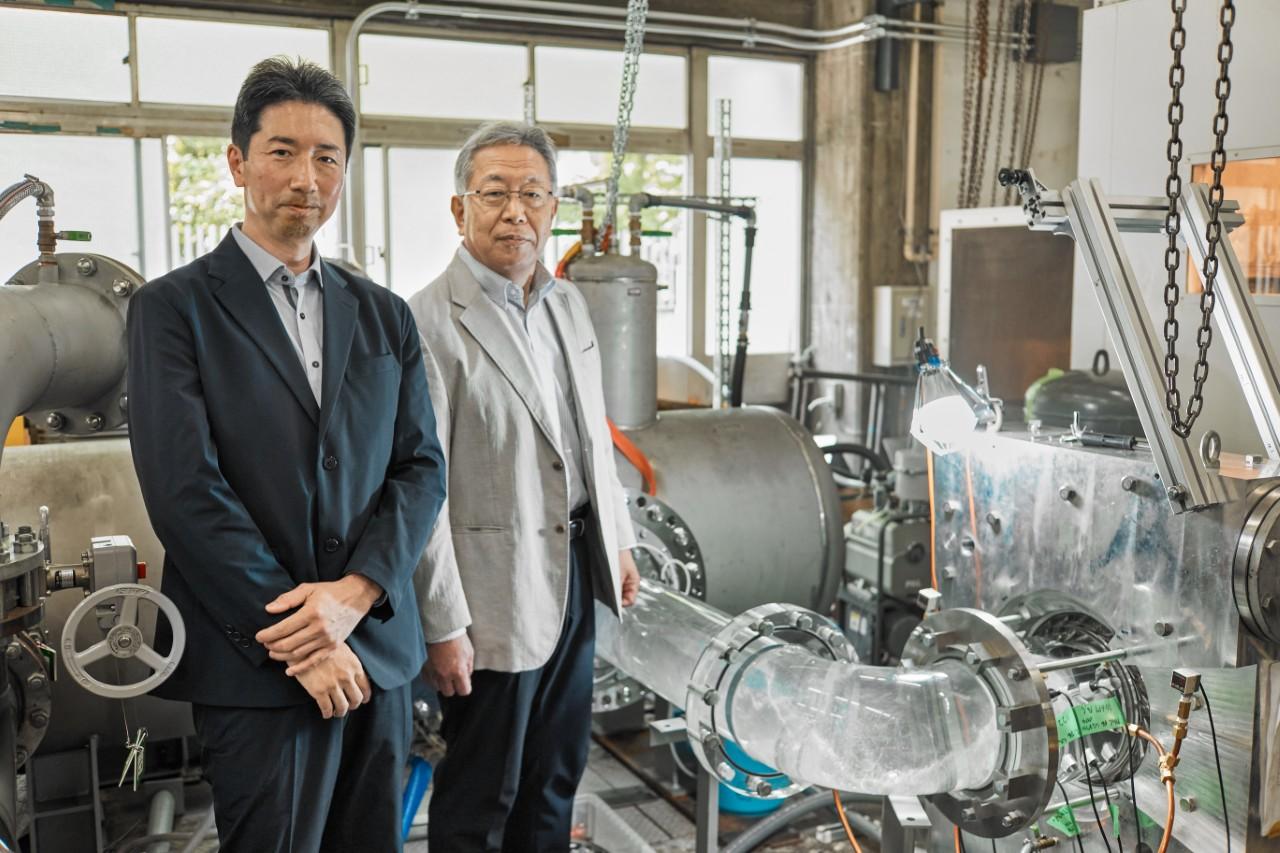
別記事で取り上げた「三浦ダム発酵食品プロジェクト」は、本プロジェクト責任者の川田が当社のさまざまなダムで実施されている貯蔵、熟成プロジェクトの先駆けとして2019年に始めた三浦ダムでの日本酒貯蔵プロジェクトが元になっているものです。興味を持たれた方は、以下の記事もぜひご覧ください。